Precision Time Protocol (PTP) for Industrial Applications: A Complete Overview
Unlock the power of Precision Time Protocol (PTP) in industrial automation. Discover its benefits, applications, and implementation for microsecond-level synchronization in manufacturing. Learn how PTP can revolutionize your industry and improve efficiency in time-sensitive networks.
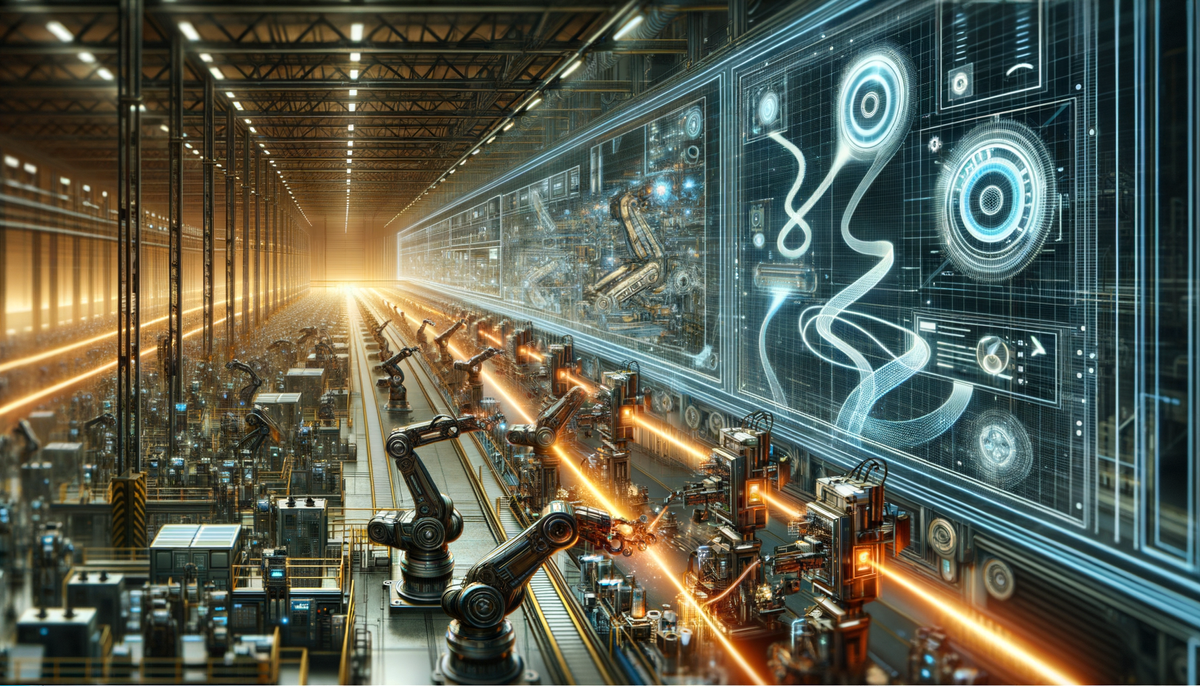
In today's fast-paced industrial world, precise timing is crucial. Enter the Precision Time Protocol (PTP), a game-changer for industrial automation and manufacturing. This article will dive deep into PTP, exploring its benefits and applications in time-sensitive networks and industry settings.
What is Precision Time Protocol (PTP)?
PTP is a highly accurate time synchronization method used in industrial networks. It allows devices to sync their clocks with incredible precision, often down to microseconds or even nanoseconds.
Key features of PTP:
- Extremely accurate time synchronization
- Designed for industrial and networked measurement systems
- Defined by the IEEE 1588 standard
- Supports various network types, including Ethernet
Why Use PTP in Industrial Automation?
Industrial processes often require precise timing for:
- Coordinating machine operations
- Logging events accurately
- Ensuring product quality
- Managing safety systems
PTP helps achieve these goals by providing a common time reference across all devices in a network.
PTP vs. Other Time Synchronization Methods
Let's compare PTP to other common time sync methods:
Method | Accuracy | Network Load | Scalability |
---|---|---|---|
PTP | Microseconds to nanoseconds | Low | High |
NTP | Milliseconds | Very low | Very high |
GPS | Nanoseconds | N/A | Limited |
As you can see, PTP offers a great balance of accuracy and scalability for industrial applications.
How PTP Works in Industrial Settings
-
Master Clock Selection:
- Devices in the network elect a master clock
- The most accurate clock becomes the master
-
Synchronization Process:
- Master sends sync messages to slave clocks
- Slaves adjust their time based on these messages
-
Delay Measurement:
- PTP measures network delays to improve accuracy
- Accounts for transmission and reception times
-
Continuous Adjustment:
- Slave clocks constantly fine-tune their time
- Ensures ongoing synchronization
PTP in Manufacturing: Real-World Examples
Example 1: Automotive Assembly Line
In a car factory, multiple robots need to work together to assemble vehicles. PTP ensures all robots are in perfect sync, leading to:
- Improved product quality
- Reduced errors and waste
- Increased production speed
Example 2: Food Packaging
A food packaging plant uses PTP to coordinate:
- Filling machines
- Sealing equipment
- Labeling systems
Result: Precise portion control and accurate expiration dates.
Example 3: Power Grid Management
PTP plays a crucial role in smart grids:
- Synchronizes power generation and distribution
- Enables accurate fault detection and location
- Supports seamless integration of renewable energy sources
Implementing PTP in Your Industrial Network
Follow these steps to set up PTP:
-
Assess Your Needs:
- Determine required accuracy
- Identify critical processes
-
Choose PTP-Compatible Hardware:
- Select switches, routers, and end devices that support PTP
-
Network Configuration:
- Enable PTP on all devices
- Configure PTP profiles (e.g., Power Profile for power systems)
-
Testing and Verification:
- Use PTP testing tools to check synchronization
- Monitor network performance
-
Maintenance:
- Regularly check PTP status
- Update firmware as needed
PTP for Time-Sensitive Networks (TSN)
Time-Sensitive Networking (TSN) is an emerging technology for deterministic Ethernet networks. PTP plays a crucial role in TSN by providing:
- Precise time synchronization
- Support for time-aware applications
- Improved network reliability
TSN use cases in industry:
- Motion control systems
- Audio/video bridging
- Industrial IoT applications
Best Practices for Industrial PTP Usage
-
Use PTP-aware network devices:
- Switches and routers that understand PTP
- Reduces timing errors
-
Implement redundancy:
- Multiple grandmaster clocks
- Alternate network paths
-
Monitor PTP performance:
- Use network monitoring tools
- Track sync accuracy over time
-
Optimize network topology:
- Minimize hops between master and slave clocks
- Use star or tree configurations when possible
-
Consider environmental factors:
- Temperature changes can affect clock accuracy
- Use temperature-compensated oscillators in harsh environments
PTP Profiles for Specific Industries
PTP profiles customize the protocol for different applications:
-
Power Profile:
- Used in power generation and distribution
- Defined in IEEE C37.238
-
Telecom Profile:
- Optimized for telecommunications networks
- Specified in ITU-T G.8265.1
-
Automotive Profile:
- Tailored for in-vehicle networks
- Described in IEEE 802.1AS
Challenges and Solutions in PTP Implementation
Common challenges:
- Network congestion
- Asymmetric delays
- Clock drift
Solutions:
- Use Quality of Service (QoS) to prioritize PTP traffic
- Implement transparent clocks to account for switch delays
- Choose high-quality oscillators for critical devices
Security Considerations for PTP
As industrial networks become more connected, securing PTP is crucial:
-
Authentication:
- Use PTP security extension (IEEE 1588-2019)
- Implement message authentication codes (MACs)
-
Encryption:
- Protect PTP messages from eavesdropping
- Use IPsec or MACsec for network-layer security
-
Access Control:
- Limit PTP traffic to authorized devices
- Use VLANs or network segmentation
-
Monitoring:
- Implement intrusion detection systems (IDS)
- Watch for unusual timing patterns or rogue master clocks
PTP and Industrial IoT Integration
PTP is becoming increasingly important in the Industrial Internet of Things (IIoT):
-
Edge Computing:
- Synchronize edge devices for real-time data processing
- Enable precise timestamping of sensor data
-
Predictive Maintenance:
- Accurately correlate data from multiple sensors
- Improve fault detection and prediction algorithms
-
Digital Twins:
- Synchronize physical and virtual models
- Enhance simulation accuracy for process optimization
Cost-Benefit Analysis of PTP Implementation
While implementing PTP requires investment, the benefits often outweigh the costs:
Benefits:
- Improved product quality
- Reduced downtime and maintenance costs
- Enhanced process efficiency
- Better compliance with industry standards
Costs:
- Hardware upgrades (PTP-compatible devices)
- Network infrastructure improvements
- Training and implementation time
ROI factors:
- Industry type and specific use case
- Current timing-related issues and their impact
- Scale of implementation
Future of PTP in Industrial Applications
As Industry 4.0 and smart manufacturing evolve, PTP will play an increasingly important role:
- Integration with 5G networks for ultra-reliable low-latency communication (URLLC)
- Enhanced support for edge computing and fog architectures
- Improved security features to protect against timing attacks
- Adaptation to quantum-based timing technologies
Conclusion
Precision Time Protocol (PTP) is a powerful tool for industrial automation and manufacturing. Its ability to provide microsecond-level synchronization across complex networks makes it invaluable for time-sensitive applications. By implementing PTP, industries can improve efficiency, reduce errors, and pave the way for next-generation smart factories.
Remember, successful PTP deployment requires careful planning, proper hardware selection, and ongoing maintenance. With the right approach, PTP can significantly enhance your industrial processes and help you stay competitive in today's fast-paced manufacturing landscape.
As we move towards more interconnected and precise industrial systems, PTP will continue to be a cornerstone technology, enabling the synchronization necessary for the factories of the future. Whether you're in automotive manufacturing, power distribution, or any other time-sensitive industry, consider how PTP can elevate your operations to new levels of efficiency and accuracy.